






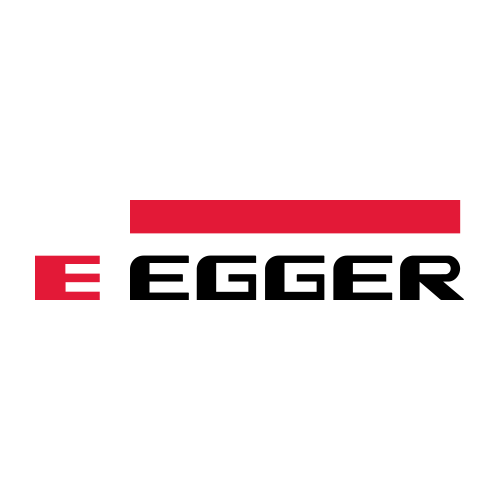
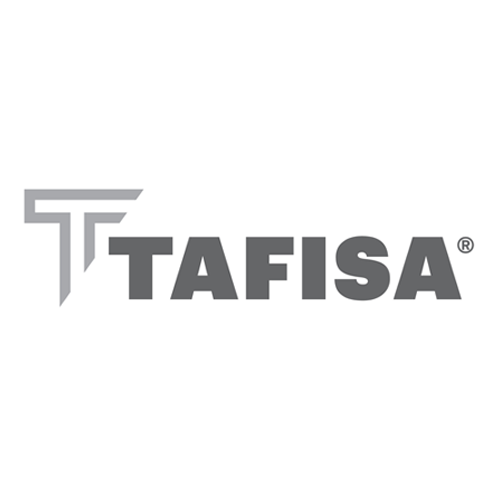
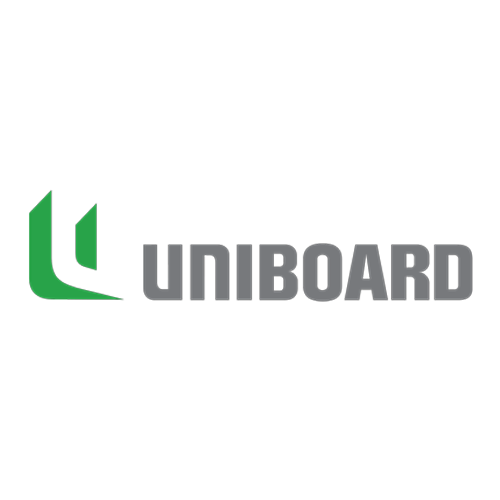
HPL
High pressure laminate panels (HPL) is the direct descendent of the original plastic laminate. It is considered to be one of the most durable decorative surface materials and is available with special performance properties including chemical, fire and wear resistance.
HPL is produced by saturating multiple layers of kraft paper with phenolic resin. A layer of printed décor paper is placed on top of the kraft paper before pressing. The resulting sandwich is fused together under heat and pressure. It is laminated to a panel utilizing a variety of adhesives. Particleboard or medium density fiberboard (MDF) are the preferred substrate because they provide a stable, durable, consistent and economical foundation. Due to its durability, HPL is a common choice for horizontal surfaces including flooring, countertops and desktops.
HPL
Laminate Description
Decorative laminate boards consist of strips of cellulose fibre (paper) impregnated with heat-hardening resins. These are joined using the manufacturing methods described below.
The coating layer generally consists of an overlay impregnated with melamine resin, decor paper and sometimes a barrier.
The core of a laminate consists of kraft paperimpregnated with phenol resin. Applying heat and pressure causes the resins to flow and subsequently cure.
Cross-linking of the resins, reinforced by the cellulose fibres of the papers, results in a very dense material with a sealed surface.
HPL
Laminate Structure
The laminate structure provides information on the number of layers of paper and their composition, in other words the laminate thickness and the quality requirements are defined. In addition to the decor paper, the number and weights of the core papers and the use of overlay and underlay are also determined
HPL
CPL process
The term CPL provides a clue to the manufacturing process; CPL is produced in continuously-operating double-belt presses with a compression force of between 30 and 70 bar and temperatures between 300 °F and 340 °F (150 °C and 170°C).
Depending on the thickness of laminate and the length of the pressing zone, the feed speed may vary from 26 to 49 ft/min (8 to 15 m/min)